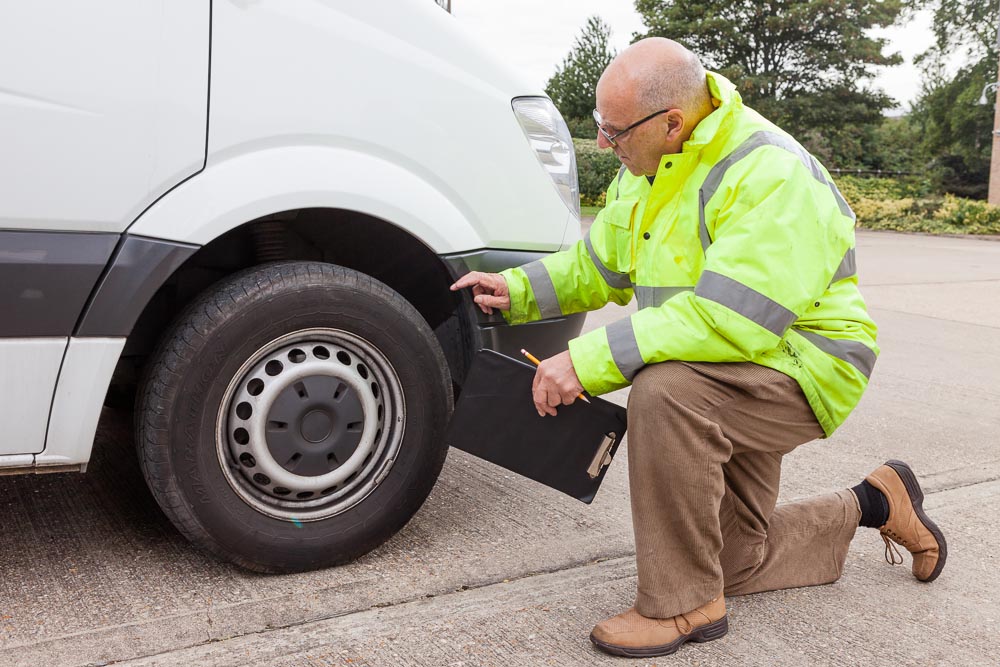
I never fail to be surprised by what I come across in my line of work. It’s a recurring theme of these features.
Take Driver Defect Reports for example.
As a Transport Compliance Auditor, I still find it astonishing how few Transport Managers check the quality of Driver Defect Reports, instead allowing drivers to conduct these with a tick-box mentality which pays lips service to this vital area of fleet control.
The Traffic Commissioners are clear on this matter:
“The DVSA still finds that between a third and a half of all prohibitable defects it finds at the roadside could have been prevented by the driver conducting an effective walkaround check. Undertaking an effective walkaround check, acting on what is found and recording that action is as much a part of a driver’s duties as steering the vehicle down the road.”
(page 9, DVSA Guide to Maintaining Roadworthiness)
Recognising that we’re all busy and short of time, the DVSA suggest three simple checks:
1. Gate Checks: When I started in the industry, many Operating Centres had Gatehouses with personnel to check collected Driver Defect Reports prior to the driver leaving. Whilst those days have gone, the modern equivalent - getting out in the yard on a random basis and overseeing the drivers doing their checks - is actually better. Radical as it sounds, you can gain more by engaging with drivers and seeing your fleet up close and personal than you ever will ever sat behind a desk. Don’t forget to record this intervention: a simple note and a signature on the driver's defect sheet is all the evidence I need as an auditor.
2. Time taken to complete a check. Most tachograph analysis software will monitor the time taken to carry out a walkaround check. Tachomaster users, for example, can use the Lead-In report, and other tachograph analysis software systems have similar reports. The report shows the time between the driver card being inserted and the vehicle moving. If this time is below 10-15 minutes, either the driver has spent insufficient time checking their vehicle or has not recorded the time which would be in contravention of tachograph regulations (care is needed if vehicles need to be moved prior to the check, for example if they are garaged in a warehouse).
3. The final check. This closes the loop. If drivers are checking their vehicle correctly, and faults are being rectified in a timely manner, there should be relatively few defects found at a Preventive Maintenance Inspection (PMI). When checking the PMI sheet, look for items which should be apparent to the driver, such as broken lights, mirrors, wiper blades, spray suppression flaps etc. This should be in addition to typically longstanding issues such as worn tyres (I’ve seen many things but never a tyre wear overnight in the yard).
Don’t be put off if you do not get results straight away.
Quality is not an act - it is a habit - and the changes will come when your actions demonstrate that you care and expect that drivers do more than just tick boxes on a form.
(Image Credit: DVSA)